80 Charlotte Street is a new office-led mixed use building for Derwent, whose story can be told through its materiality, expert craftsmanship, bespoke processes, techniques and quality. For despite its large scale, when you look deeper this is a building that has been made by 'hand'.
Our client, Derwent London, is renowned for their design pedigree and portfolio of innovative, design-led commercial projects and a commitment to quality and craft. The ambition for 80 Charlotte Street was to create a building of distinction, that was unashamedly contemporary but also expressed the heritage and character of Fitzrovia. The Lead Architect was Make Architects, with AFK Delivery Architect.
Working closely with a variety of specialist firms and craftspeople, a palette of handmade materials and finishes was developed to create an elegant, calm and contextual aesthetic. Natural materials such as stone, concrete, brick and timber were selected for not only their variety of texture, but for their subtle, natural imperfections which in turn convey a sense of time, process and bespoke craftsmanship. AFK's role was to preserve the 'handmade' qualities of the unique materials set out in the schematic design, and to develop efficient and innovative systems and processes for installing them safely and swiftly at scale.
The site was formerly the home to global advertising giants Saatchi and Saatchi, so as a homage to this the architectural language and composition of the building is strikingly graphic, bold and uncluttered. Externally, the building’s facades feature a handmade grey brick from Petersen Tegl’s factory in Denmark, inspired by the controlled, yet organic poured in-situ concrete envelope of the David Zwirner Gallery on 20th Street in New York, and
the shuttered concrete interiors of Denys Lasdun’s National Theatre in London. A darker charcoal brick was used on the park side elevation to create contrast and drama. A sculptural Corten steel canopied entrance announces the building on the street - a portal form fabricated in Como and inspired by the artist Donald Judd, with its changing texture, colour and patina adding a sense of human scale and enclosure at the point of entry.
The interiors also feature black polished concrete floors, exposed concrete soffits, expressed black steel columns and beams, and beautiful timber flooring. Textured board-marked concrete spandrels surround two dramatic atria which are flooded with daylight, with warm specialist leather upholstery by Bill Amberg forming booths and seating areas.
Below we celebrate some of the materials and makers that have helped create this extraordinary, crafted building:
Brick
Brick was chosen for much of the new building's façade, for its tactile and organic aesthetic that could weave easily into Fitzrovia's fabric. Petersen Tegl, founded in 1791, is the only brickworks in Denmark which still coal fires its bricks. This traditional process, which takes three days, gives each brick a unique colouring, glaze, and mottling across the surface. Hand-made 'Kolumba' bricks were selected for 80 Charlotte Street are made by pressing a wet lump of clay into a wooden mould, and each feature their maker's two thumb prints imprinted at either end where they are lifted out of the mould. Although these marks are hidden when the bricks are in situ, they remain part of the building’s story.
Working with non-uniform bricks on such a large building was a challenge but AFK developed a system of setting these handmade bricks into panels, so they could quickly and safely, without the attenuate risks of handsetting. As the brick are set over a large area, the subtle blend of shades with all its indents and irregular marks creates a beautiful and richly textured façade.
Weathered steel
The building’s double-height Corten entrance canopy is inspired by artist and sculptor Donald Judd who often worked with the material. Corten steel features dramatic colours and a textured surface of blisters and pockmarks which emerge as the steel rusts during the oxidation process. Weathered steel continues to rust and changes colour until it reaches its peak patina at around two to four years. The joint between the steel box frame entrance portal and the concrete façade is deliberately suppressed to create the impression that the steel box has been 'punched' through into the concrete exterior in as a single sculptural element. Although it appears to be a simple four-sided box, the portal is highly complex internally, with an intricate sub-layer beneath the surface which house rainwater channels, intercom support and other functions. Working with such a complex and unpredictable materials takes skill and craftsmanship, demonstrated on this project by leading modular steel manufacturer, Metalsistem, based in Italy and Félix, highly specialised architectural envelope designers based in Switzerland.
Shuttered concrete
Two thirds of the new building, both internal and external is shuttered pre-cast concrete panels, inspired by Denys Lasdun’s use of the material in his 1960s National Theatre. The shuttered concrete was made by casting concrete panels in timber moulds to produce a finish with a pronounced wood grain, imperfections and subtle colour variations. To get exactly the right finish, rigorous testing and prototyping was required, with full scale mock-ups built of the external panels, to test the colour variations, chips and mottles that would be created by the timber moulds.
After several prototypes had proved too smooth, a soap mix was developed to release the concrete panels from the wooden forms which produced just the right amount of texture and grain details, giving the external panels a rugged finish. Internally, glass reinforced concrete was used, just 10% of the weight of regular concrete. Again, panels were rigorously tested and eventually cast from a rubber mould taken from selected sandblasted timber with a softened grain. In both processes, imperfections are harnessed to create texture, tactility and subtle visual variations.

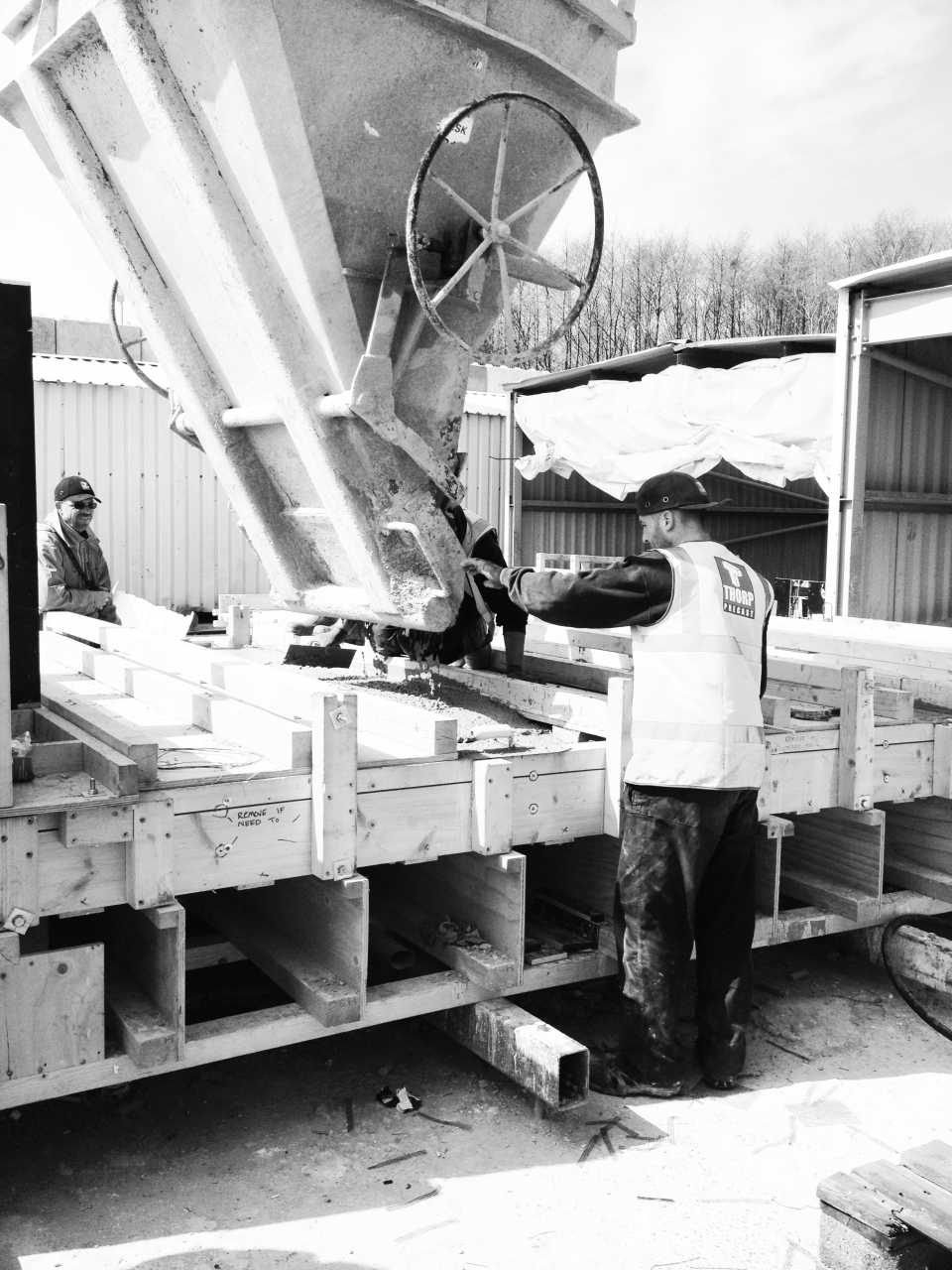
Blackened concrete
Elegant blackened concrete floors run through the new building, contrasting with the textured concrete walls and wooden floors of the main atria, and acting as the backdrop for activity in the building's ancillary spaces, lift lobbies and receptions. The floor was inspired by the 150sqm floor of Hamilton’s Gallery in Mayfair which serves as a dramatic but neutral backdrop to the gallery’s photographic exhibitions. Made by London-based master craftsmen Lazenby, the concrete features a stain that is added whilst it is poured. It is then burnished by hand, with the trowel marks clearly visible, along with lines and subtle stripes of colour where the stain is worked through the concrete. Each Lazenby floor is unique, individual and contemporary, combining a sleek, polished surface with the imperfections that are the hallmark of a handmade finish. Beautiful and highly reflective, they can also withstand robust footfall.
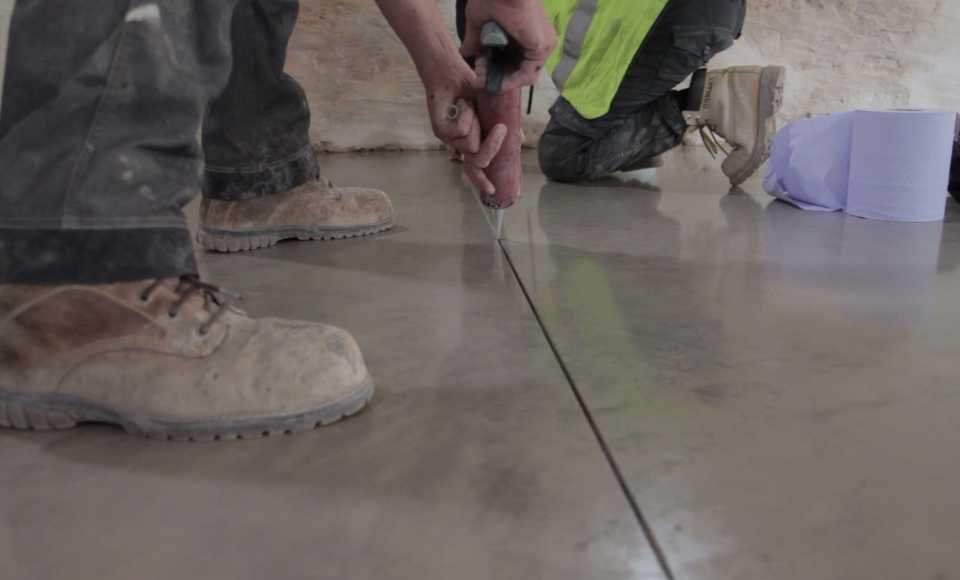

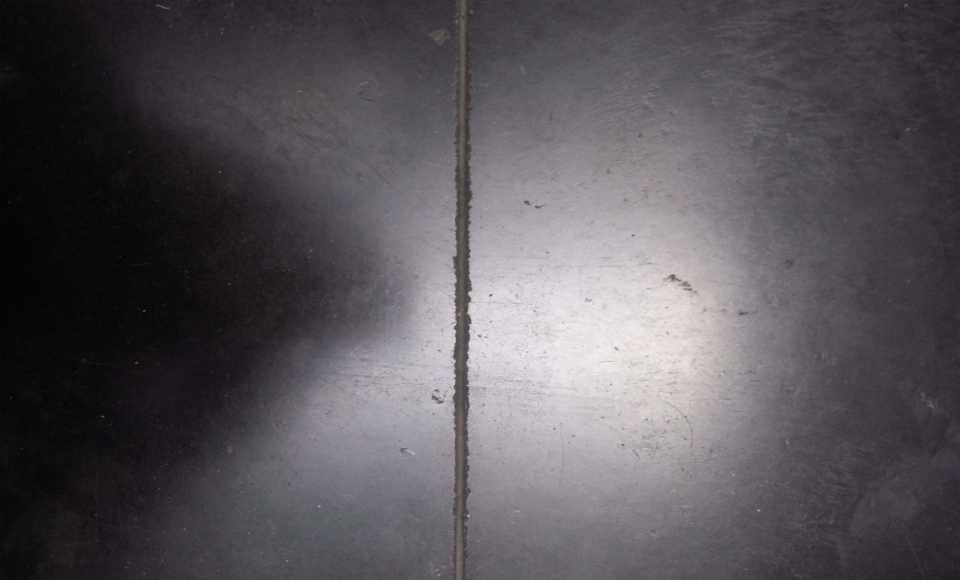
Leather
Bill Amberg Studio is a specialist artisan leather crafts workshop in London, whose work features in several of Derwent London’s buildings. Established for over 30 years, Bill Amberg Studio employs architectural leatherworkers and artisans from the worlds of saddlery and bookbinding to explore the aesthetic possibilities of leather.
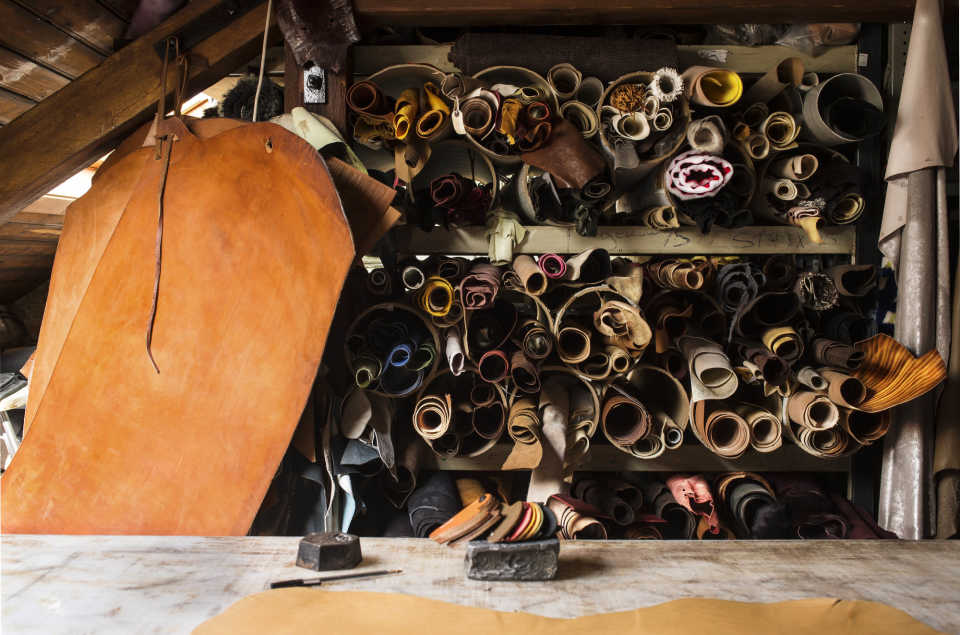

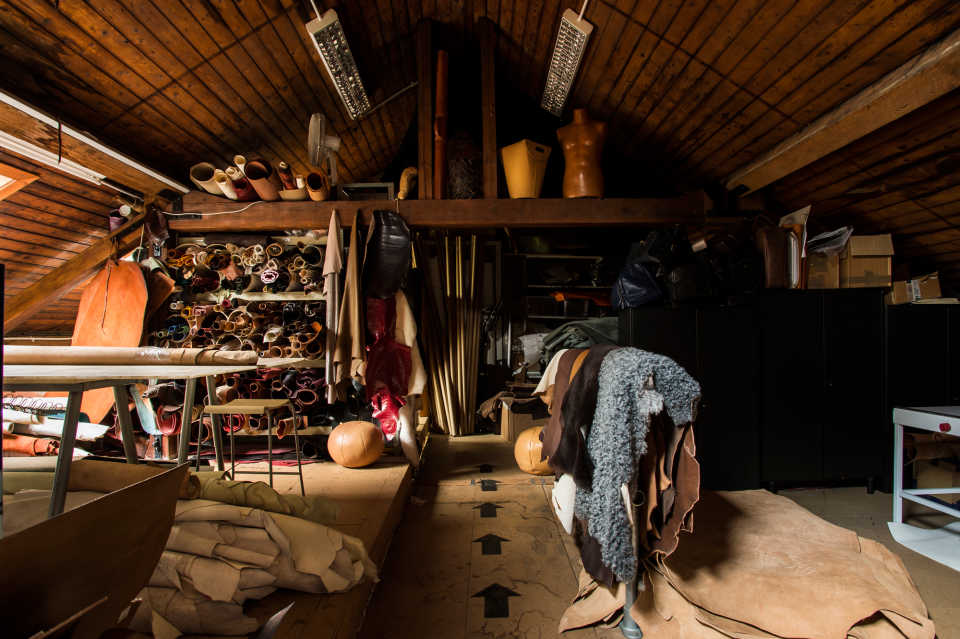
In keeping with the weathered rugged look of the building, Amberg's Studio celebrates the tangible history of a hide, relishing the marks and blemishes which might tell of insect bites, scars, or grazes where the animal has brushed up against a barbed wire fence; stories with make each piece of leather unique. Amberg's leather features a number of smaller, informal spaces including recessed booths in 80 Charlotte Street's reception and café, with leather horseshoe seating. The booths are warmly lit to create more intimacy within the grand expanse of the atria, and to highlight the texture and character of the leather.
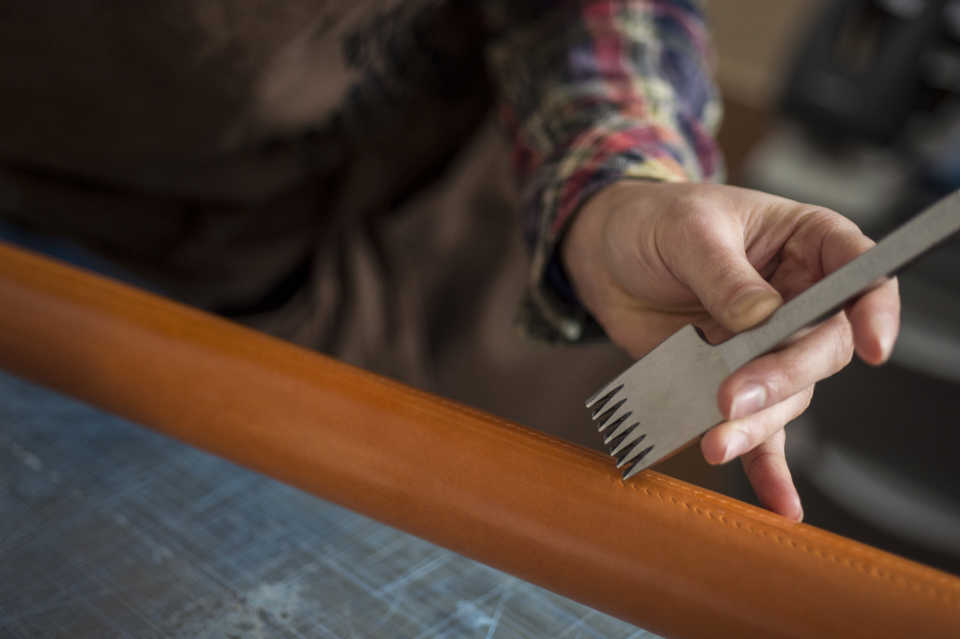
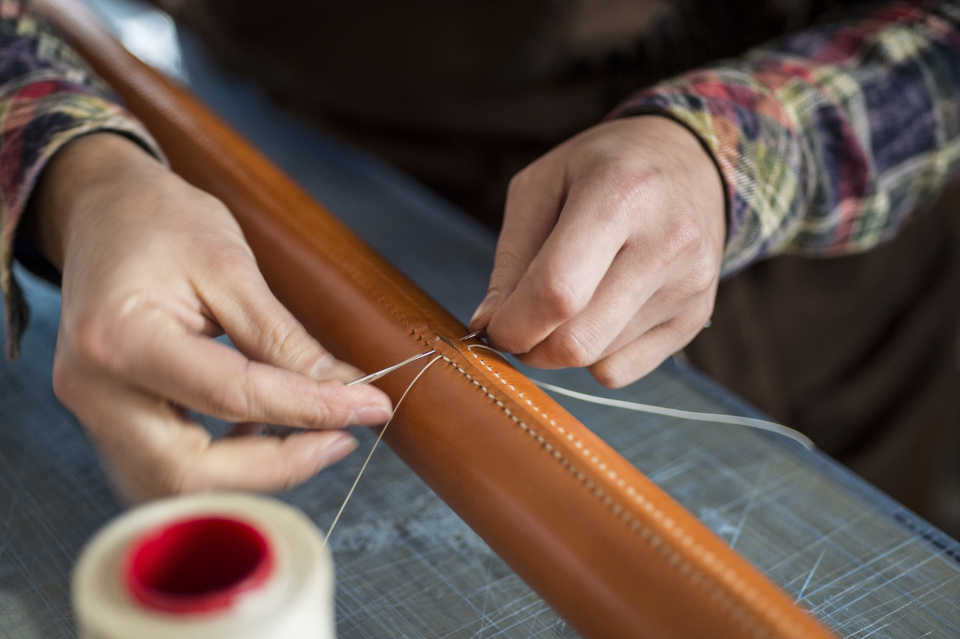
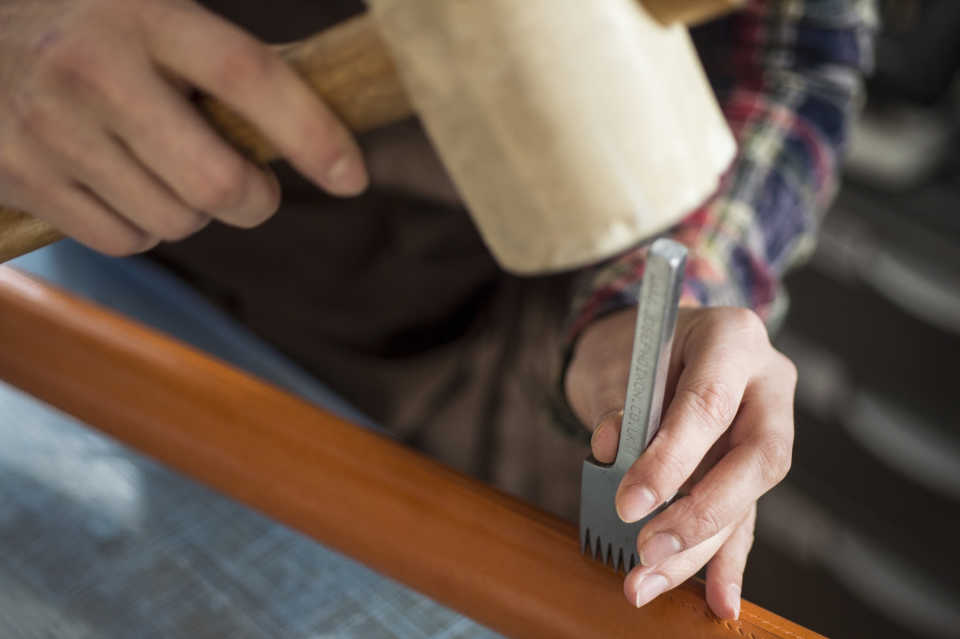
Wood
The soaring central atrium and reception space features an expansive but intricately detailed wood floor by Dinesen. Danish experts in bespoke timber flooring., Dinesen work primarily with Douglas Fir and Oak, sourced from Germany's Black Forest. Dinesen’s unique process means that trees, once felled, are left in the forest in the same spot for a year to slowly air dry and prevent warping, before being taken to the factory. Dinesen’s process respects and preserves the trees’ knots and imperfections, believing that they are testimony to the history and vitality of the tree.
A dramatic Douglas Fir floor features in the main atria of the new building, its planks displaying the distinctive character of the tree, and where repairs have been made to split planks and where large knots were removed. The textured grain of the flooring echoes the imprint of the wood from the moulds used to create the interior boarded concrete panels, implying a harmonious dialogue between materials.
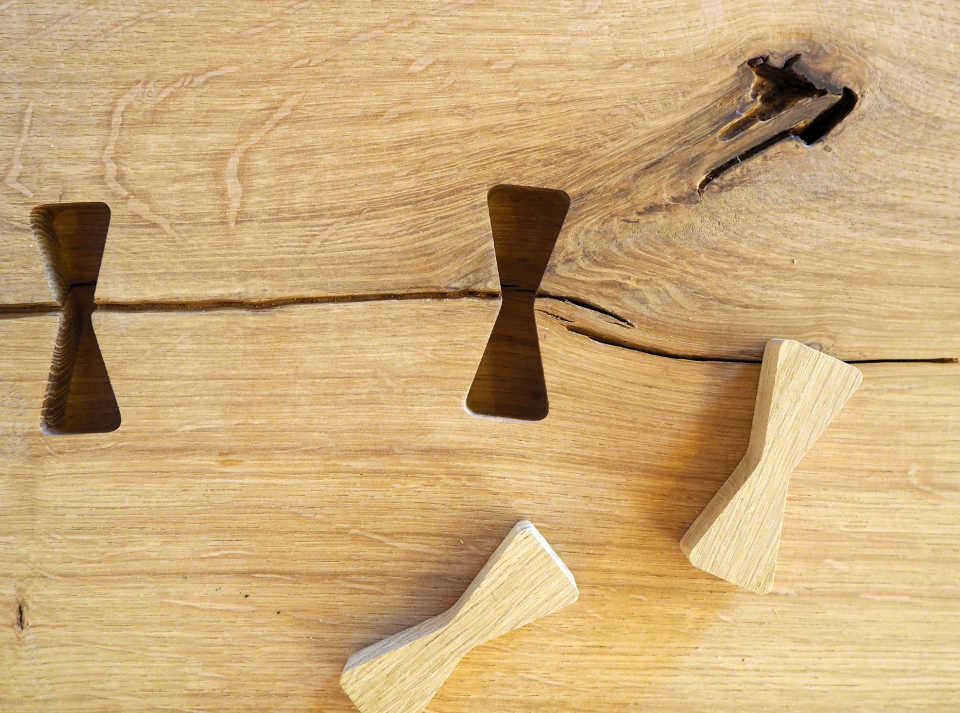
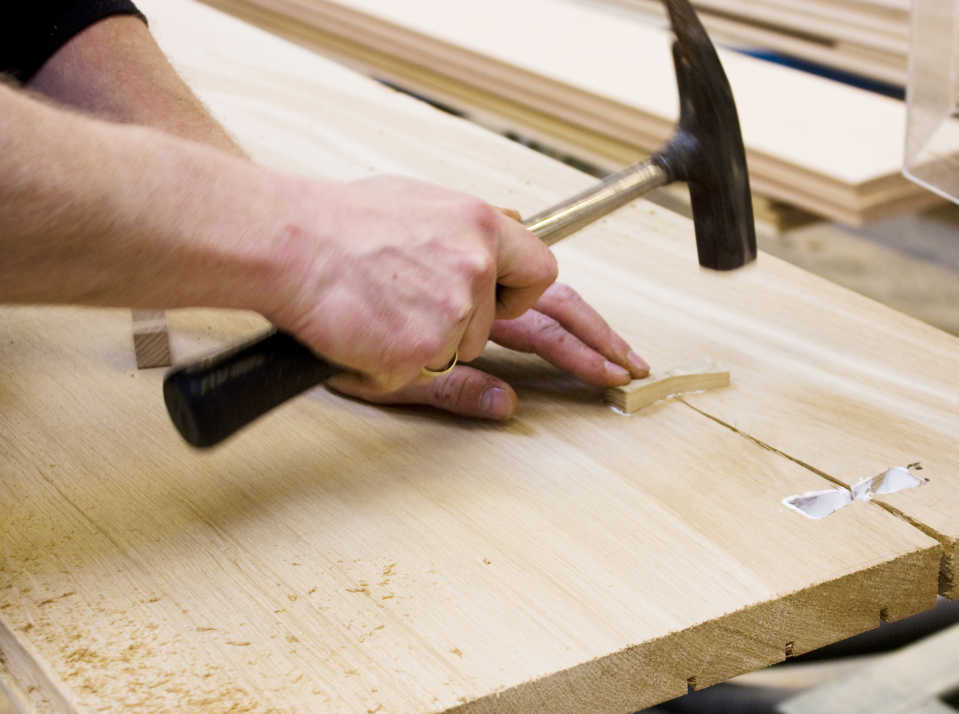

- End -
'Handmade' - the story of 80 Charlotte Street is also a publication by AFK. The hardcopy book was published by traditional hand bookbinders Bookworks, and is available on request. Photography is reproduced here with kind permission from Derwent, Bill Amberg Studio, Dinesen, and Petersen Tegl. The Lead Architect was Make Architects, with AFK Delivery Architect